Digitalisation is often equated with automation. People think of jobs disappearing because robots or other machines replace human work. But if you take a closer look, the situation is completely different. Digitalisation and automation differ fundamentally.
Prof. Emil Schubert
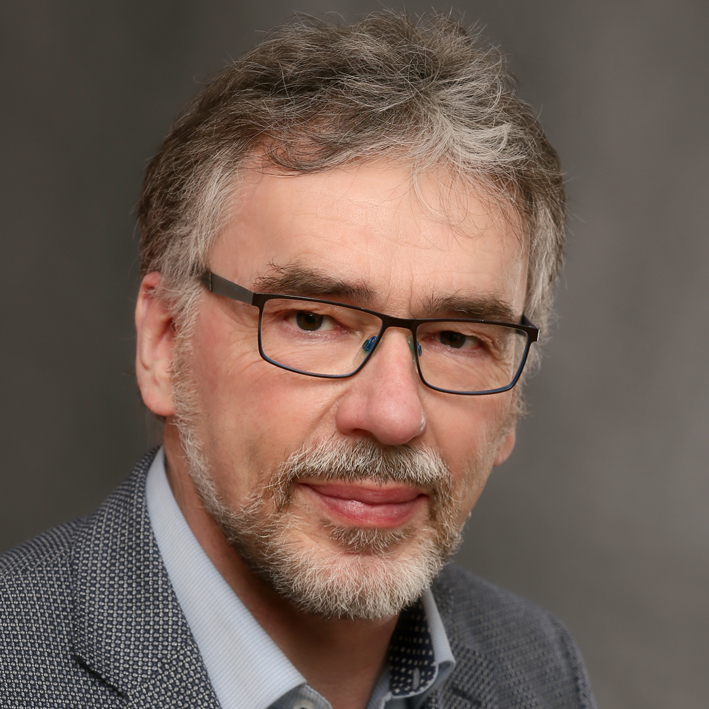
Recent Posts
How does digitalisation affect welding technology?
Topics: automation, research & development
Laser welding: first expert talk in the Weld Lounge
When two experts discuss a subject, it can be very interesting and exciting. Sharing this exchange with as many people as possible who are thirsty for knowledge is very close to my heart. For this reason, I would like to offer a new format to all interested persons: the Weld Lounge. In the Weld Lounge, I welcome top-class discussion partners from the diverse world of welding on a wide range of specialist topics.
Topics: research & development
Sustainable welding? Guaranteed with this welding cell!
The fact cannot be denied: Potential skilled workers choose their employer according to the level of sustainability of the company. But you can't make an omelette without breaking eggs. This also applies to welding. ABICOR BINZEL has developed the "clean" arc welding cell with the support of TWI (The Welding Institute) Cambridge. This cell demonstrably enables low-emission, energy-saving and raw material-saving production.
Topics: automation, research & development
Why is narrow-gap welding sustainable?
Pipeline construction, shipbuilding, tank construction – where thick sheets are welded together, the welding equipment is put to the test. Several layers of filler metal have to be applied on top of each other and the extreme heat development puts additional strain on the welding equipment. Those who can use narrow-gap welding for this purpose really do act sustainably.
Topics: automation
Sustainability in welding – is that possible?
You can't make an omelette without breaking eggs. Every manufacturing company uses natural resources in some way and thus affects the environment. But modern companies must position themselves sustainably. Besides the ecological aspect, there is another important fact: potential skilled employees choose their employer according to its sustainability concept. Thus, if you want to keep up with the competition, you can no longer avoid the topic of sustainability. But how can a production company that uses welding technology in its processes approach the issue of sustainability at all?
Topics: Health & Safety, research & development
What makes tactile seam tracking so special in laser joining?
In the past, and to some extent still today, resistance spot welding is used in car body construction to join metal sheets. If, for example, a vehicle roof has to be joined to a side panel, the welding robots place many welding points next to each other in this process. Jokingly, this is sometimes referred to as "stapling". Basically, this process is still a suitable joining method, but restrictions with regard to car body design as well as the general technical development partly required alternative solutions.
Topics: research & development
How does laser welding work?
Nowadays, laser welding has long been a standard process, which is used, for example, in automobile production, steel construction as well as in the aerospace industry. The principle of laser welding is "light amplification by stimulated emission of radiation" and means that light is generated with only one wavelength. The high energy density of 105 up to 106 Watts per square centimetre generated in this way is exploited technically in welding: the high energy density of a laser beam is applied to a small spot, creating the possibility of contactless welding at high process speed.
Topics: automation, research & development
Joining technology trends 2023
Developing and producing companies of joining technology are just as excited about the trends in their industry for 2023 as distributors and users themselves. Exhibiting companies as well as visitors are eagerly awaiting the start of the international trade fair for joining, cutting and coating technology SCHWEISSEN & SCHNEIDEN 2023 – which returns to its old location in Essen this year. A lot has happened since the last exhibition in 2017. Prof. Dr. Emil Schubert – the WELDPROF® – presents the changes or reinforcements that will take place next year from his point of view.
Topics: research & development
What was going on with the WELDPROF in 2022?
A close look will certainly reveal that the WELDPROF® is now officially a registered trademark – Congratulations! For six months now, the ABICOR BINZEL CTO Prof. Dr. Emil Schubert has been out and about as a personal brand, bringing the diversity of welding technology closer to all interested parties through his knowledge as a Professor of Joining Technology, Materials Scientist and Doctor of Laser Technology.
On tour with the WELDPROF to the night of technology
The Hans Viessmann school, a vocational school in Northern Hesse, about 60 kilometres away from ABICOR BINZEL's headquarters, had attracted about 80 interested people to a night full of technology on December 7, 2022. Technicians, industrial foremen, lecturers/teachers and of course interested vocational students attended the event. Of course, the WELDPROF® alias Prof. Dr. Emil Schubert could not miss such a night!
Topics: On Tour